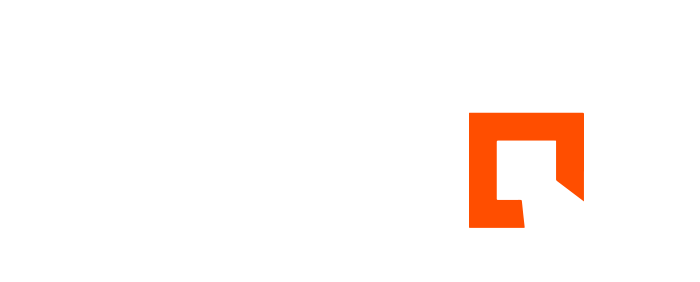
Thousands of jobs, all right here.
5,656
Great jobs available, right now.
Filtering
City +
- Albany (56)
- Avon (30)
- Becker (59)
- Belgrade (11)
- Big Lake (88)
- Brooten (7)
- Clear Lake (7)
- Cold Spring (108)
- Elk River (459)
- Elrosa (1)
- Foley (22)
- Holdingford (7)
- Kimball (17)
- Melrose (57)
- Paynesville (36)
- Rice (48)
- Richmond (8)
- Rockville (18)
- Saint Cloud (2075)
- Saint Joseph (78)
- Saint Martin (9)
- Sartell (188)
- Sauk Centre (96)
- Sauk Rapids (255)
- Unavailable (35)
- Waite Park (154)
Companies +
- 7-Eleven (2)
- 7-Eleven, Inc. (7)
- A&B Welding & Construction Inc (1)
- AB Staffing Solutions (2)
- AbbVie (1)
- ABC Legal Services (1)
- Abc Supply (1)
- Abercrombie & Fitch Co. (4)
- Abercrombie and Fitch (3)
- ABM Industries (1)
- ABM Industries, Inc. (1)
- Acara Solutions (19)
- Access Healthcare (1)
- Accra (1)
- Accurate Home Care (1)
- ACCURATE HOME CARE, LLC (1)
- Acosta (4)
- Acosta Group (5)
- Actalent (11)
- Adams Publishing Group LLC (1)
- Adams Publishing, Inc (1)
- Adara Home Health (3)
- Advance Auto Parts (5)
- Advance Stores Company Inc (2)
- Advanced Comfort Health (1)
- Advantage Solutions (1)
- Adzuna (1)
- Aegis Therapies (5)
- AEO (2)
- Aeon (2)
- Aequor Allied (2)
- Aerotek (40)
- AEROTEK INC (2)
- Affinity Plus Federal Credit Union (2)
- Ag Tech Drainage (1)
- AGSTAR FINANCIAL SERVICES, ACA (1)
- AIM Transportation Solutions (1)
- Aimbridge Hospitality (1)
- Air Evac Lifeteam (1)
- Albany Area Gymnastics (1)
- Albany Area School District 745 (1)
- Albany Area Schools (19)
- Aldi (3)
- Aleron (7)
- All Medical Personnel (1)
- AllCare Medical Services (4)
- Allied National Services (2)
- Allied Universal (7)
- Allina Health (1)
- Alternative Senior Care (1)
- Amazon (1)
- Amazon DSP Driver (1)
- AMAZON WORKFORCE STAFFING (6)
- Amazon.com Services LLC (1)
- Amcon Concrete Products, LLC (2)
- American Cybersystems, Inc (1)
- American Family Insurance (1)
- American Greetings (1)
- American Greetings Corporation (1)
- American Red Cross (1)
- American Traveler (2)
- Ameripride Services, Inc. (2)
- Ames Construction, Inc. (4)
- AMPI (4)
- AmSurg Corp. (2)
- Anders Group (4)
- Andersen Corp. (7)
- Andersen Corporation/Renewal by Andersen (3)
- Anderson Trucking Service (14)
- Anderson Trucking Service, Inc. (4)
- Anonymous (3)
- Anywhere Real Estate (1)
- Apex Service Partners (2)
- Applied Industrial Technologies (2)
- Applied Industrial Technologies - Dixie, Inc. (1)
- Aramark (2)
- Aramark Corporation (2)
- Arby's (2)
- Ardor Health Solutions (2)
- Army National Guard (1)
- Arvig Enterprises, Inc. (3)
- Aspen Dental (2)
- Associated Milk Producers (1)
- Associated Milk Producers Inc (1)
- Associated Wholesale Grocers (3)
- Assurant (1)
- Assured Nursing, Inc. (3)
- AT&T (1)
- Atlas Staffing (2)
- Atlas Staffing Inc (13)
- Atterro (2)
- Augusta plumbing and heating (7)
- Auto Club Group (2)
- Automotive Parts Headquarters, Inc. (12)
- Automotive Parts Solutions Inc (1)
- AutoZone, Inc (3)
- Aveanna (1)
- Aveanna Healthcare (6)
- Avenue Staffing Inc (1)
- Axelon Services Corporation (1)
- Aya Healthcare (Staffing) (6)
- Aya Healthcare, Inc. (21)
- Aya Locums (2)
- B & B Hoffman Sod Farms Inc (1)
- BAS HealthCare (1)
- Bath & Body Works (1)
- Bath & Body Works, LLC (1)
- Bayada Home Health Care (2)
- Bayada Nurses (4)
- Bayer Built Woodworks (1)
- BC Forward (1)
- BC Forward $21.42 per hour (1)
- BCforward (1)
- BCG Attorney Search (1)
- BCI CONSTRUCTION, INC. (6)
- BDS Connected Solutions (1)
- Beacon Hill Staffing Group, LLC (1)
- Beacon Hill Staffing Group, LLC $110,000.00 - $150,000.00 per year (1)
- Beacon Hill Staffing Group, LLC $35,000.00 - $55,000.00 per year (1)
- Beacon Roofing Supply, Inc. (1)
- Beaudry Oil & Propane (1)
- Beaudry Oil and Service, Inc (4)
- Beaudry Oil Co & Service Inc (1)
- Beauty Barrage (1)
- Becker Public Schools (11)
- Beeline Group (1)
- Ben's Structural Fabrication, Inc. (1)
- Benedictine (9)
- Benedictine Health System (18)
- Benton County (1)
- Bernick's (10)
- Best Buy (4)
- Big lake (1)
- Big Lake Public Schools (22)
- Bimbo Bakeries Usa, Inc. (1)
- Bimbo's Bakeries USA (1)
- BioLife Plasma Services (2)
- Blattner Company (19)
- Blaze Credit Union (1)
- Bluestone Physician Services (5)
- BMS CAT (7)
- Bolton & Menk, Inc. (2)
- Border Foods (1)
- Border States (1)
- Border States Electric Supply (2)
- Border States Industries (1)
- Boser Construction Inc (2)
- Boys & Girls Clubs of Central Minnesota (15)
- Braun Intertec $39,600.00 - $59,400.00 per year (1)
- Braun Intertec $48,000.00 - $72,000.00 per year (1)
- Braun Intertec Corporation (8)
- Breakthru Beverage Group (1)
- Brenny Transportation Inc (1)
- Bridgestone Americas (1)
- Bright Spring Services (1)
- Brightspring Health Services (3)
- Bristol Myers Squibb (1)
- Bristol Myers Squibb Mexico (1)
- Brothers Market (1)
- Buckhead Minnesota (6)
- BUFFALO WILD WINGS (1)
- Bureau Veritas (1)
- Burlington (2)
- C. R. England (1)
- C.H. Robinson (1)
- C.R. England - Dedicated Routes (1)
- Caleres, Inc. (3)
- Capital One (2)
- Capital One Financial Corp. (4)
- Capstone Logistics (2)
- Capstone Logistics, LLC (1)
- CARAVEL AUTISM HEALTH (2)
- Cardinal Comfort Care Cooperative (1)
- Care Medical Supply Inc (1)
- Care.com (8)
- Career Search Associates, Inc. (1)
- Cargill (7)
- Cargill Incorporated (6)
- Carhop (1)
- Carlson & Stewart Refrigeration (3)
- Carolina Beverage (1)
- Carter's/Oshkosh (3)
- Carter's, Inc (2)
- CASSIA (2)
- Catholic Charities (4)
- Catholic Charities of the Diocese of Saint Cloud (16)
- Catholic Charities of the Diocese of St. Cloud (9)
- Catholic Community Schools (3)
- CCL Hospitality Group (1)
- CDI Custom Curb Adapters (2)
- CDLLife (1)
- Center for Diagnostic Imaging (4)
- Centerspace (3)
- Centerwell (1)
- CENTIMARK CORPORATION (1)
- Centracare (24)
- Centracare Clinic (2)
- CentraCare Cold Spring Clinic (1)
- CentraCare Health (209)
- CentraCare Health System (4)
- Central Heating & Air Conditioning (1)
- Central Minnesota Credit Union (5)
- Central Minnesota Legal Services (2)
- Central Minnesota Mental Health Center (23)
- CenturyLink (1)
- Cetera Financial Group (32)
- Charter Communications (1)
- Chartwells K12 (1)
- Chipotle Mexican Grill, Inc. (2)
- Christianson PLLP (3)
- CHS Inc. (2)
- Chuck E. Cheese (4)
- Cintas (5)
- Cintas Corporation (15)
- Circle K (3)
- City Of Elk River (3)
- City of St. Cloud (5)
- City of St. Cloud Minnesota (7)
- Claires Stores, Inc. (1)
- CliftonLarsonAllen (2)
- Climate Express (2)
- Climate Express, Inc. (3)
- Club Demonstration Services (1)
- CMG - Corporate Office (1)
- Coborn's, Inc. (48)
- Coborn's Incorporated (118)
- Coffee & Bagel Brands (13)
- Coffee and Bagel Brands (1)
- Cognizant Technonology Solutions (1)
- Coldspring (9)
- Collabera Inc. (2)
- College of Saint Benedict & Saint Johns' University (17)
- College Of Saint Benedict And Saint John's University (8)
- College of Saint Benedictsaint John's University (2)
- College of St Benedict (3)
- College Town (1)
- Collyard Chiropractic P.A. (1)
- Colorful Concepts Painting & Custom Finishing (1)
- Comfort Keepers of St. Cloud, MN (2)
- Community Options, Inc. (1)
- CommunityGiving (1)
- Companions Animal Hospital (1)
- Compass Group North America (3)
- COMPASS GROUP USA INC (1)
- Compeer Financial (1)
- CompHealth (8)
- CONCRETE INC (1)
- ConnectAbility of MN (1)
- Copart (1)
- Core & Main Lp (2)
- Core Medical Group (1)
- Core-mark (2)
- CoreMedical Group (2)
- Cornerstone Auto Group Llc (3)
- Cornerstone Building Brands (2)
- CorTech LLC (1)
- COST CUTTERS (3)
- Country Manor Campus (23)
- County Of Sherburne (4)
- Cretex Companies (1)
- Cretex Companies, Inc. (1)
- CRH (3)
- CrossMark (7)
- Crothall (1)
- Crst The Transportation Solution (2)
- CRST The Transportation Solution, Inc. (1)
- Crystal Distribution (3)
- Culligan of Sauk Centre (1)
- CVS Health (4)
- CWMF Corporation (1)
- CyberCoders (4)
- Cynet Health (2)
- Dahl Consulting Inc. (16)
- Dairyland Peach (2)
- DART (1)
- DaVita Healthcare Partners (1)
- Dayton Freight LInes, Inc. (4)
- Del Hayes and Sons, Inc. (1)
- Department of Agriculture (1)
- Department of Veterans Affairs (19)
- DeZURIK, Inc. (13)
- Dick's Sporting Goods, Inc. (1)
- Diedre Moire Corporation (1)
- Dinges Fire Company (1)
- Diocese of Saint Cloud (10)
- Direct Jobs (1)
- DirectEmployers (1)
- Dish (1)
- DOHERTY (39)
- Doherty Staffing (3)
- Doherty Staffing Solutions (1)
- Doherty Staffing Solutions Inc. (10)
- Dollar General (7)
- Dollar Tree (11)
- Dollar Tree Stores, Inc. (1)
- Dominium Management Services, Inc. (1)
- Domino's (24)
- DoorDash (3)
- Driveline (8)
- DSW Inc. (1)
- dubow textile (5)
- Dungarvin (2)
- Dycom (6)
- E-Clan, Inc. (1)
- E. A. Sween Company (1)
- Eagle Creek Renewable Energy LLC (1)
- EAGLE_EYE (1)
- Eastey Enterprises (1)
- Ebenezer (7)
- Ebenezer Cares (2)
- Eckroth Music (2)
- Eclaro International, Inc. (1)
- Ecolab (1)
- Ecumen (19)
- Eden Senior Care (2)
- Edward Jones (3)
- Electrical Builders (3)
- Elior North America (1)
- Elk River Public School District (85)
- Ellie Mental Health (3)
- Emergent Financial Group (7)
- Emerson Electric Co. (1)
- Entegee (1)
- Enterprise Holdings (2)
- Enterprise Medical Recruiting (1)
- Enterprise Mobility (2)
- ENTRUST Solutions Group (2)
- Epic Healthcare Staffing (4)
- Epic Travel Staffing (2)
- Ericsson (1)
- Essilor (11)
- Essilor and Subsidiaries (2)
- ESTES EXPRESS LINES (3)
- Evenson Decker, PA (1)
- EVOLVE Family Services (1)
- Exaways Corporation (1)
- Express Employment Professionals (2)
- Fairview Health Services (8)
- family support services (1)
- FAR Inspections (3)
- Farmers Insurance Agency Owner Location (2)
- Farmers Union Industries, LLC (1)
- Fastenal Company (2)
- Fastenal Company Inc (4)
- FAVORITE HEALTHCARE STAFFING, INC. (15)
- FedEx Freight (3)
- FedEx Ground (1)
- FedEx Services (2)
- FEDEX TRADE NETWORKS (3)
- Ferche Millwork Inc. (5)
- Firestone Complete Auto Care (2)
- Five Below (2)
- Fleet Farm (2)
- Fleetpride, Inc. (1)
- FlexCare (2)
- Focus Staff (1)
- Foley Public Schools (1)
- Food Safety and Inspection Service (1)
- Fortrex (1)
- Fraser (8)
- Fresenius Medical Care (2)
- Fresenius Medical Care North America (5)
- Fresh Thyme Farmers Market (5)
- Fresh Thyme Farmers Markets (1)
- Fresh Thyme Market (3)
- Frontera Search Partners (1)
- FURNITURE MART USA (9)
- Fusion HealthCare Staffing (2)
- Fusion Medical Staffing (6)
- Fusion Medical Staffing-Cath Lab (2)
- Fusion Medical Staffing-Radiology (1)
- Fusion Medical Staffing-Therapy (1)
- Fusion Medical Staffing, LLC (1)
- G4S (1)
- Gamestop Corp. (4)
- GATR Truck Center (11)
- Genie Healthcare (7)
- Geo-Comm (2)
- Geo-Comm, Inc. (1)
- Gerber Collision (1)
- Gerhardson Chiropractic (1)
- Get It Rite Construction LLC (1)
- GetMed Staffing, Inc. (3)
- Girl Scouts of Minnesota & Wisconsin Lakes and Pines (1)
- GLC On the Go (1)
- Global Medical Staffing (1)
- GNC (1)
- GO Healthcare Staffing (2)
- Good Samaritan Society (1)
- Good Shepherd Campus (13)
- Goodguys Motor Co (1)
- Goodin Company (1)
- Goodwill Industries-Easter Seals (1)
- Goodwill-Easter Seals of Minnesota (1)
- GPAC (2)
- Granite City Brewery (1)
- Great Clips (2)
- Great Clips, Inc. (12)
- Great Lakes Management Company (1)
- Great River Federal Credit Union (1)
- Great River Regional Library (1)
- Great Theatre (3)
- Grede (1)
- Grede Holdings (1)
- Green Fox LLC (2)
- GREEN THUMB (4)
- Green Thumb Industries (6)
- GROOME TRANSPORTATION (2)
- Grundfos (3)
- Guardian Angels Senior Services (30)
- Guardian Pharmacy (5)
- Gustave A. Larson Company (1)
- GXO Logistics (1)
- Hallmark Marketing Corporation (2)
- Hand & Stone (1)
- Hasbro (2)
- Health Advocates Network-Allied (2)
- HEALTH INVENTURES, LLC (4)
- Healthcare Recruitment Counselors (1)
- Healthcare Services Group (2)
- Healthcare Services Group, Inc. (3)
- HealthCare Traveler Jobs (1)
- HealthPartners Services Inc. (1)
- HealthPartners, Inc. (4)
- Hearing Healthcare Recruiters (1)
- Heartland Glass Co., Inc. (1)
- Heartland Veterinary Partners (1)
- Helping Hand Companions, Inc (1)
- Helzberg Diamonds (2)
- HERC- Upper MidWest (33)
- Hershey Company (1)
- Hinnenkamp Dairy, Inc. (1)
- Hirschbach Motor Lines (2)
- HOBBY LOBBY STORES (1)
- Hobby Lobby Stores, Inc. (1)
- Hog Slat, Inc. (1)
- Holdingford Public Schools (1)
- Hom Furniture, Inc. (2)
- Home Instead (1)
- Homegoods (1)
- Homewatch Caregives (1)
- HonorVet Technologies (1)
- Horizon Roofing Inc (3)
- Horizontal Talent (1)
- Hormel Foods (9)
- Host Healthcare (5)
- Housing and Redevelopment Authority of St. Cloud, MN (1)
- HRT SOLUTIONS (1)
- Humana (2)
- I State Truck Inc (1)
- Ichor Systems (40)
- Independent Community Bankers of America (1)
- Independent School District 742 Comm Schools (46)
- INFOJINI (1)
- Inh Properties (2)
- Insomnia Cookies (2)
- Instacart Shoppers (1)
- Interstates Construction Services, Incorporated (3)
- Intuit (1)
- IRET Apartments (4)
- Iret Properties Lp (1)
- Irvine Technology Corporation (ITC) (1)
- ISC Healthcare (1)
- ISI Trading, Inc. (2)
- J.C. Penney Company, Inc. (1)
- J&R Schugel Trucking, Inc. (1)
- J&J Family of Companies (1)
- J&R Schugel Trucking (1)
- JBS (8)
- JBS USA (1)
- Jd Home Healthcare (6)
- Jennings Well Drilling Inc (1)
- Jerry's Food (1)
- Jimmy John's (1)
- Jobot (1)
- John Deere (2)
- JOHNSON BROTHERS (1)
- Johnson Controls, Inc. (1)
- JonnyPops (1)
- Journeys (1)
- JPMorgan Chase & Co. (3)
- K&B Transportation (1)
- Kane Transport (1)
- Keefe Commissionary Network LLC (1)
- Kelly Services (6)
- Kelly Services, INC. (5)
- Kerry (2)
- Keurig Dr Pepper (3)
- Kimball Area Schools (1)
- Kimmel and Associates (1)
- Knife River (5)
- Knife River Corp (25)
- Knife River Materials (17)
- Knute Nelson (1)
- Kohl's (2)
- KPG Allied (2)
- KWIK TRIP INC (34)
- Kwik Trip/Kwik Star (1)
- La-Z-Boy Inc. (5)
- Lakeside Foods (1)
- LAKESIDE FOODS INC (7)
- LANCESOFT (2)
- LAND O'LAKES (1)
- Land O'Lakes, Inc. (13)
- Landform Professional Services LLC (1)
- Largeton Inc (1)
- Lauridsen Group Inc. (2)
- Law Firm Staff (1)
- Lazer Spot (1)
- Leaf Home (3)
- Leaffilter (7)
- Learning Care Group (4)
- Learning Care Group, Inc. (6)
- Learning Tree Child Development Center (2)
- LeFebvre Companies (2)
- Legacy Restoration (3)
- Lenscrafters (4)
- LGI Homes (1)
- Liberty Diversified International (1)
- LIberty Paper Inc. (3)
- Liberty Personnel Services, Inc . (2)
- Lids Inc (2)
- LIFESPARK (2)
- Lifesprk (4)
- LINDE (5)
- Linde Gas & Equipment Inc (2)
- Live Trucking (4)
- Louis Industries Inc (1)
- Love's Travel Stops & Country Stores (11)
- Loves Travel Stops & Country Store (2)
- Loving Hands Transportation (1)
- LRS Healthcare - Allied (1)
- Lucid Staffing Solutions (2)
- Lunds & Byerlys (3)
- Lutheran Social Service Of Minnesota (1)
- Lutheran Social Service Of Mn (15)
- Luxottica (10)
- LUXOTTICA OF AMERICA INC (16)
- Lyman Lumber Company (1)
- Macy's, Inc. (1)
- Macy's (1)
- magnifi financial (1)
- MAGNIFI FINANCIAL CREDIT UNION (4)
- Magnum (1)
- Mains'l (1)
- Malone Healthcare - Nursing (1)
- ManpowerGroup (5)
- Manufacturing Partners Inc (1)
- Marco (3)
- Marco Technologies (1)
- Marten Transport (6)
- Martin Marietta Materials (2)
- Mary T Inc (1)
- Maselter Cabinets (1)
- Massage Envy (9)
- MasTec Network Solutions (1)
- Matrix Medical Network (2)
- MATRIX PROVIDERS (1)
- Mayo Clinic (5)
- McDonald's (1)
- MDO Periodontics PA (1)
- Medtronic (3)
- Meduit (1)
- MedWave Healthcare Staffing (3)
- Menards (5)
- MENARDS, INC. (2)
- Metal Craft (9)
- Metal Craft Machine and Engineering (5)
- Metal Craft Machine Engineering (1)
- Metro Bus (4)
- Metro Dentalcare (1)
- Metro Sales Inc (2)
- Metropolitan Council (1)
- michaels (7)
- Michels Corporation (4)
- MicroBiologics (10)
- Microbiologics Inc. (1)
- Mid-Minnesota Cold Storage, LLC (2)
- Mid-Minnesota Legal Aid (1)
- Midco (4)
- Midcontinent Communications (4)
- Midland Credit Management (1)
- MidMinnesota Legal Assistance (2)
- Midwest Machinery Co. (7)
- Millennium Health (2)
- Millerbernd (5)
- Millerbernd Manufacturing Co. (6)
- MILLS FLEET FARM (4)
- Minnehaha County (3)
- Minnesota City Jobs (1)
- Minnesota Credit Union Network (1)
- Minnesota Department of Human Services (5)
- Minnesota Judicial Branch (1)
- Minnesota Paving & Materials (4)
- Minnesota State (57)
- Minnwest Bank (2)
- MissionCare (1)
- MN Sherburne County Jail (7)
- MNS1 Express Inc (1)
- Moments Hospice (7)
- Momentum Truck Group (1)
- Monarch Healthcare Management (4)
- MONROE OPERATIONS (5)
- Moran Transportation (2)
- Morris Midwest (1)
- Morris Midwest, LLC (1)
- MPQ Inc (1)
- Mr. Cooper (1)
- Nahan Printing (28)
- National Dentex (3)
- National Guard (5)
- National Staffing Solutions-Surgical Services (1)
- National Vision (4)
- Naven Health (1)
- Navy (1)
- NDX Thoele (3)
- New Flyer (10)
- New Season (1)
- Newport Healthcare (11)
- Next Move Healthcare (3)
- Nexus (2)
- Nightingale Nurses - Allied (1)
- NIKE INC (1)
- Noodles & Company (7)
- North Memorial Health Care (3)
- Northrop Grumman (2)
- Northrop Grumman Corporation (2)
- NORTHWEST RESPIRATORY SERVICES (1)
- Novelty, Inc. (1)
- NRG Energy, Inc. (1)
- Nueces County (1)
- Nurses First Solutions (2)
- Nutrien (3)
- Nutrien Ag Solutions (5)
- Nystrom & Associates, Ltd (8)
- Nystrom Residential Treatment, LLC (1)
- O'Reilly Automotive Inc (6)
- Oakley (3)
- Oakley Trucking (2)
- Old National Bank (2)
- OLD NAVY (1)
- Oldcastle (5)
- OldCastle APG (1)
- Oldcastle Inc. (1)
- OMG Midwest, Inc (2)
- OneStaff Medical (7)
- Opatz Metals, Inc. (1)
- OPENTABLE (1)
- Operating Company","category":"Category","country":"Country","city":"City","state":"State","hireType (1)
- Opportunity Matters, Inc (1)
- Optum (6)
- Orkin, Inc. (1)
- Orlando Health (7)
- OSL Retail (1)
- OSL Retail Services (1)
- Osl Retail Services Inc (1)
- Oxygen Service Company (1)
- OXYGEN SERVICE COMPANY, INC. (1)
- Palmer Group (3)
- Panda Restaurant Group, Inc (2)
- Pandora Group (1)
- Panera (1)
- Papa Murphy's Midwest (6)
- Papa Murphys Franchisees (1)
- Paper Transport (2)
- Paychex (2)
- Pearle Vision (1)
- PENSKE (3)
- Penske Truck Leasing (2)
- Peopleready (8)
- Per Mar Security Services (1)
- Performance Food Group (17)
- Performance Foodservice (15)
- Petco (2)
- Petco #602 (4)
- Pflipsen Farms, LLC (1)
- Phoenix School Counseling (1)
- Pilgrim's - 3.4 (1)
- Pilgrim's USA (1)
- Pilgrims (12)
- pilot company (1)
- Pilot Flying J (3)
- Pimco (1)
- Pinnacle Climate Technologies (1)
- Planet Healthcare (2)
- Polar Tank Trailer LLC (3)
- POMP'S TIRE SERVICE INC (2)
- Pomp's tire Service (1)
- PrairieCare (2)
- Preferred Credit, Inc. (4)
- Premier Medical Staffing Services (3)
- Premier Medical Staffing Services, LLC (2)
- Premise Health (1)
- PRIDE Health (3)
- Prime Communications (1)
- Prime Healthcare Staffing (3)
- Prime Physicians (2)
- PRIME STAFFING (2)
- Prime Time Healthcare LTC (1)
- Pro Resources (1)
- Pro Staff (1)
- Pro Talent Crafter (1)
- ProBuild Company LLC (1)
- Product Connections (1)
- Professional Diversity Network (10)
- ProMedica Senior Care (1)
- Propio Language Services (2)
- ProtoCall Services (1)
- Proxi Dental Staffing (1)
- Pulse Healthcare Services (2)
- Quanex (2)
- Quanex Building Products Corporation (10)
- Quinlivan & Hughes, P.A. (2)
- R.E. Michel Company, Inc. (1)
- R&M Manufacturing Co. (6)
- Radco Truck Accessories (1)
- Rain For Rent (4)
- Raising Cane's (2)
- Rasmussen College (4)
- RAYUS Radiology (4)
- RBC Bearings (1)
- RDO Equipment (8)
- RDO EQUIPMENT CO. (4)
- Reading & Math, Inc. (1)
- Red Robin (5)
- Redneck Trailer Supplies (1)
- Regional Diagnostic Radiology (2)
- Regional Health Center (1)
- Regions Financial Corporation (1)
- Regis Corporation (4)
- RehabVisions (1)
- RELX Group (1)
- RENEGADE TRUCK EQUIPMENT INC (3)
- Renewal by Andersen (1)
- Rentokil North America (2)
- Republic Services (2)
- Retail Merchandising Services (2)
- Retina Consultants of Minnesota (2)
- Rice Companies, Inc. (2)
- Ridgemont Resources, Inc. (1)
- Rihm Kenworth (2)
- Rileighs Outdoor LLC (Vogel Display Corp) (1)
- River City Dental (1)
- River of Life Church (3)
- Riverside Farms (1)
- RMS (1)
- Robert Half (15)
- Rocori Public Schools (7)
- Roehl Transport (8)
- Rogers (1)
- Rollins, Inc. (2)
- Ross Stores, Inc. (3)
- Rotochopper, Inc. (9)
- Royal Tire (1)
- Royal Tire, Inc. (1)
- S J Louis (1)
- Safelite Auto Glass (1)
- Saint Cloud Hospital (1)
- Saint Cloud State University (1)
- Saint Cloud, MN (3)
- Sally Beauty Holdings (2)
- Salvation Army (3)
- Sam's Club $16.00 - $23.00 per hour (7)
- Sam's Club $17.00 - $24.00 per hour (2)
- Sam's Club $18.00 - $25.00 per hour (2)
- Sam's Club (10)
- Sandpiper Brands (1)
- Sandpiper Productions (1)
- SARGENTO (1)
- Sartell-St. Stephen Independent School District 748 (13)
- Sartell-St. Stephen School District (1)
- SAS Retail Services (1)
- Sauk Rapids Public School District (3)
- Savers / Value Village (1)
- Savers Thrifts Stores (1)
- SCHEELS (20)
- Schneider (1)
- School Administrative Unit #19 (1)
- SCHUSTER (1)
- Schwan’s Home Delivery (1)
- SCR (7)
- Select Comfort Corporation (1)
- Select Medical (4)
- Select Medical Corporation (1)
- SENIOR HELPERS (1)
- ServiceMaster MN Professional Services (1)
- Sevita (19)
- Shaffer Trucking (1)
- Shared Medical Services (2)
- Sherburne County (6)
- Sherwin-Williams Co. (1)
- Sherwin-Williams Company (2)
- Shields Health Solutions (3)
- ShiftMed (2)
- Shipt (2)
- Shopko Stores Operating Co, LLC (1)
- Short Elliott Hendrickson Inc. (5)
- Showcase Dance Studio (1)
- Shutterfly (1)
- Signify Health (1)
- Sisters Of The Order Of Saint Benedict (2)
- Skechers (3)
- SkillXChanges (1)
- SkyBridge Healthcare Therapy (1)
- Skyline Med Staff Allied (4)
- SKYVIEW (1)
- SMARTSTYLE (1)
- Sola Optical (4)
- Soliant (1)
- Solutions Behavioral Healthcare Professionals (2)
- SonderMind (1)
- Sorenson Communications Llc (1)
- Sorenson Communications, Inc. (3)
- Source Medical, LLC. (1)
- SPANIER WELDING & METAL FABRIC (1)
- SPAR Inc. (3)
- Spartannash (4)
- Spectrum (7)
- Spectrum High School (10)
- Spectrum HighMiddle School (1)
- Spee Dee Delivery Service, Inc. (13)
- SPENCER'S GIFTS (3)
- Spire Federal Credit Union (2)
- SportClips (3)
- Springboard Healthcare (2)
- SpringPath Mental Health Services (7)
- SRS Merchandising (1)
- SST Direct (1)
- St Cloud Area School District 742 (14)
- St Cloud Ear, Nose, Throat Clinic Pa (1)
- St Cloud Family Dental (1)
- St Cloud Technical & Community College (6)
- ST CROIX HOSPICE LLC (1)
- St. Cloud Hospital (1)
- St. Cloud Municipal Athletic Complex (1)
- St. Cloud School District 742 (38)
- St. Cloud State University (82)
- St. Cloud Technical and Community College (1)
- St. Croix Hospice (3)
- St.cloud (1)
- Stability HealthCare (4)
- Staff Management | SMX (1)
- StaffDNA (2)
- Staffmark (6)
- Staffmark Group (2)
- Standard Iron & Wire Works (5)
- Standard Iron & Wire Works, LLC (2)
- Stanley Black & Decker (1)
- Stanley Black & Decker, Inc. (2)
- Stanley Black and Decker (2)
- Stantec (10)
- Starbucks (2)
- Starbucks Coffee Company (10)
- State of Minnesota (20)
- Statewide Remodeling (1)
- Stearns Bank (2)
- Stearns County (2)
- Stearns Electric Association (1)
- STERIS (1)
- Steris Corporation (3)
- Structural Buildings (1)
- Stryker (1)
- Stryker Corporation (1)
- Subway - 34611-0 (1)
- Subway - Sauk Centre (1)
- Summit Fire Protection (2)
- Summit Medical Staffing (4)
- Summit Medical Staffing Nursing (2)
- Sun Crest Tax Service (1)
- sunbelt (2)
- Sunbelt Staffing Solutions Inc (1)
- Superprof (1)
- Surface Preparation Technologies LLC (1)
- Surgery Care Affiliates (1)
- Surgical Care Affiliates (1)
- Surgical Care Affiliates, LLC (3)
- Svihel Vegetable Farm, Inc (1)
- Synagro Technologies (1)
- Syngenta (1)
- Sysco (9)
- SYSCO CORP (3)
- Sysco Western Minnesota (14)
- Sysco Western Minnesota, Inc. (1)
- T Mobile USA Inc. (3)
- T-Mobile (7)
- Taco Bell (5)
- Tactical Advantage LLC (1)
- Talkspace (1)
- Target (12)
- Target Corporation (1)
- TEKsystems (1)
- TEKsystems c/o Allegis Group (1)
- Telcom Construction (3)
- TelCom Construction, LLC (6)
- Terminal Transport, Inc. (1)
- The Bank of Elk River (2)
- The Buckle (5)
- The College of St. Scholastica (1)
- The Dental Specialists (1)
- THE ESTEE LAUDER COMPANIES (1)
- The Good Shepherd Community (1)
- THE HERSHEY COMPANY (1)
- The Home Depot (1)
- The Lauridsen Group (2)
- The Mentor Network (2)
- The Sherwin-Williams Company (1)
- The Vision Companies (1)
- The Vitamin Shoppe (1)
- Thies & Talle Management Co Inc (1)
- Thies u0026 Talle Management (1)
- THMED (1)
- Thrivent Financial (1)
- Thrivent Financial for Lutherans (1)
- Titan Medical Group (3)
- TJ Maxx (4)
- TKC Holdings, Inc (1)
- TLC University (1)
- Toppan Merrill Llc (2)
- Toppers Pizza (1)
- Torrid (1)
- TOTALMED (3)
- TotalMed Allied (3)
- TotalMed Staffing (1)
- Towne Nursing / Towne Healthcare (1)
- Townsquare Media (3)
- TR Concrete, Inc (2)
- Tractor Supply Company (2)
- Tradesmen International (1)
- Tradesmen International, Inc. (2)
- TRAUT COMPANIES (4)
- Travel Nurses, Inc. (1)
- Travelers Insurance Company (3)
- Tri County Action Program (2)
- Tri-County Action Program (Tri-CAP) (4)
- Triage (3)
- Triage Staffing (3)
- TriCom Technical Services (1)
- Trillium Staffing (1)
- Trinity Services Group Inc. (1)
- Trobec's Bus Service, Inc (1)
- Trobec's School Bus Service (4)
- TRS Healthcare (3)
- TRUDELL TRAILERS (1)
- TrueBlue Inc. (1)
- Trustaff (2)
- Trustaff Allied (2)
- TruStone Financial (1)
- TSA (1)
- Tutored by Teachers – Joveo Programmatic (1)
- Twin City Staffing LLC (6)
- U-Haul (9)
- U.S. Bank (1)
- U.S. Customs and Border Protection (1)
- U.S. Foodservice, Inc. (1)
- U.S. Vision (1)
- U.S. Xpress (1)
- U.S. Xpress Teams Dedicated (1)
- ULTA Salon, Cosmetics & Fragrance, Inc. (6)
- Ultimate (1)
- UMPhysicians (1)
- United Rentals, Inc. (2)
- United Way of Central Minnesota (4)
- Unitedhealth Group (4)
- Uniti Med (1)
- UnitiMed (1)
- University Of Minnesota (2)
- University of Minnesota Medical School (1)
- University of Minnesota Physicians (1)
- US Bank (1)
- US Foods (1)
- US Foods, Inc. (1)
- US Veterans Health Administration (2)
- Utilities Service, LLC (1)
- Valvoline (3)
- Varsity Tutors (1)
- vbeyond corp (1)
- Veit & Co Inc (1)
- Ventura Medstaff (1)
- Verizon Communications Inc. (2)
- Verizon Wireless (2)
- Vestis Corporation (2)
- Vestis Services (2)
- Veterans Affairs, Veterans Health Administration (10)
- Veterans Health Administration (8)
- Vetted (1)
- Viking Client Services, LLC (1)
- Viking Coca-Cola (27)
- VISION TRANSPORTATION (1)
- VitaminShoppe (1)
- Viva USA, Inc. (2)
- Vivian Health (1)
- Vivint (1)
- Vivo HealthStaff (1)
- Vogel Display Corp (1)
- Vontier (2)
- Wal-Mart Stores, Inc. (1)
- Walgreens (4)
- WALGREENS COMPANY (12)
- Walmart (83)
- Walmart $112,000.00 - $197,000.00 per year (1)
- Walmart $14.00 - $26.00 per hour (16)
- Walmart $14.00 - $33.00 per hour (4)
- Walmart $14.00 per hour (3)
- Walmart $16.00 - $36.00 per hour (4)
- Wapiti Medical Staffing (1)
- Warning Lites (1)
- Waste Management (17)
- Waste Management Corporation (1)
- Water guards (1)
- Wayfair (1)
- Wayne Transports,Inc (1)
- WellPath (10)
- Wellpath / Correct Care Solutions (2)
- Wells (13)
- Wells Concrete (7)
- Wells Concrete Products Company (7)
- Wells Fargo (5)
- WELLS FARGO & COMPANY (2)
- Wellspring Nurse Source (5)
- Westaff (9)
- Westrock (1)
- WestRock Company (3)
- Westwood Professional Services (8)
- Westwood Professional Services Inc (3)
- What Would Bri Do dba Bri's Lodge (1)
- White Cap (2)
- Winston Retail (1)
- Winters Solutions LLC (1)
- Wireless Vision, LLC (1)
- WIS INTERNATIONAL (4)
- WM (2)
- WM (Formerly Waste Management) (2)
- Wolters Kluwer (13)
- Wright Medical Group (1)
- WSB & Associate Inc (3)
- WSB & Associates, Inc. Dba WSB (3)
- Xcel Energy (3)
- XPO Logistics, Inc (1)
- YMCA of St. Cloud (9)
- YMCA of the North (9)
- Your Boat Club LLC (1)
- Yrc Freight (3)
- Zack Group (3)
- Zarminali Pediatrics (2)
- Zeiss (1)
- ZEISS Group (1)
- Ziegler Cat (2)
- Ziegler Inc. (3)
- Zimmerman Physical Therapy (1)
- ZOLL LifeVest (1)
- Zoll Medical Corporation (1)
Type +
Source +
- 17060Employment Type: Full-Time, Onsite Segment: EducationBrand: K-12-by-EliorState: Minnesota (US-M (1)
- 7-Eleven, Inc. (7)
- ABC Legal Services (1)
- ABC Supply (1)
- Abercrombie & Fitch Co. (4)
- ABM Industries, Inc. (1)
- aboutjobs (7)
- aboutjobs US (1)
- Acara Solutions (14)
- Acosta (4)
- Adara Home Health (2)
- ADCI HYD 13 SEZ (1)
- Advance Auto Parts (5)
- Advance Stores Company Inc (2)
- AEO (2)
- Aeon (2)
- Affinity Plus Federal Credit Union (1)
- AgHires (3)
- AgStar Financial Services, ACA (1)
- Aimbridge Hospitality, LLC (“Aimbridge”) (1)
- ALBANY AREA SCHOOLS (19)
- All Truck Jobs (11)
- Allied Universal (2)
- AllRetailJobs (8)
- Alternative Senior Care (1)
- Amazon.Com Llc - A03 (1)
- Amazon.com Services LLC (1)
- Amcon Concrete Products, LLC (2)
- American Composites Manufacturers Association (1)
- American Family Insurance (1)
- American Greetings Corporation (1)
- American Public Works Association (1)
- American Red Cross (1)
- American Thoracic Society Inc (1)
- Ameripride Services, Inc. (2)
- Andersen Corporation/Renewal by Andersen (3)
- Anderson Trucking Service (14)
- Anywhere Real Estate (1)
- Applied Industrial Technologies - Dixie, Inc. (1)
- ARAMARK Corporation (2)
- Arby's (2)
- Artistic Image Hair & Nail Salon (1)
- Asian jobs (1)
- Association of International Certified Professional Accountants - CIMA (1)
- Atlas Staffing Inc (13)
- Attorney Jobs in USA (2)
- AudiologyOnline (1)
- Augusta plumbing and heating (7)
- AUTOjobs.com (1)
- Automotive Parts Headquarters, Inc. (12)
- Autozone, Inc. (2)
- Aveanna Healthcare (4)
- Aya Healthcare (Staffing) (6)
- B&K Trucking Inc (1)
- Barefoot Student (16)
- Bath & Body Works, LLC (1)
- Bayada Nurses (4)
- Bayer Built Woodworks (1)
- Bcg Attorney Search (1)
- BCI Construction Inc (6)
- BDS Connected Solutions (1)
- Beacon Roofing Supply, Inc. (1)
- Beauty Barrage (1)
- Behr Sales LLC (1)
- Benedictine Health System (18)
- Bernick's (9)
- Best Buy (3)
- Bimbo Bakeries Usa, Inc. (1)
- BioLife Plasma Services (1)
- Blattner Company (8)
- Blind (1)
- BluePipes (16)
- Bluestone Physician Services (2)
- Border States Industries (1)
- Boyd (1)
- Boys & Girls Clubs of Central Minnesota (9)
- Braun Intertec Corporation (8)
- Brewery.Work (2)
- BreweryJobs.com (1)
- Bristol Myers Squibb Mexico (1)
- Brother's Market (1)
- Bureau Veritas (1)
- Burlington (1)
- C.H. Robinson (1)
- Caleres Inc. (3)
- Capital One Financial Corp. (4)
- Capstone Logistics (2)
- CARAVEL AUTISM HEALTH (2)
- Career Circle (2)
- Career Force (668)
- Career Search Associates, Inc. (1)
- CareerBuilder (62)
- CareerMD.com (13)
- Careers in Food (US) (2)
- Careers In Grocery (2)
- CareersinCannabis.com (3)
- Careersingear (3)
- Cargill, Incorporated (6)
- Carter's, Inc. (2)
- CASSIA (1)
- Catholic Charities of the Diocese of Saint Cloud (16)
- Catholic Community Schools (3)
- CCL Hospitality Group (1)
- CDL Job Now (4)
- CDLjobs.com (1)
- CentraCare Health (204)
- Central Minnesota Credit Union (5)
- CENTRAL MINNESOTA MENTAL HEALTH CENTER (23)
- Cetera Financial Group (31)
- Chartwells K12 (1)
- Chipotle Mexican Grill, Inc. (2)
- Christianson PLLP (3)
- CHS Inc. (1)
- Chuck E. Cheese (1)
- Cintas Corporation (14)
- CITY OF ELK RIVER (3)
- City of St. Cloud Minnesota (7)
- Claires Stores, Inc. (1)
- CliftonLarsonAllen (1)
- Coborn's, Inc. (47)
- Coffee & Bagel Brands (13)
- COLDSPRING (5)
- Collabera Inc. (2)
- College of Saint Benedict & Saint Johns' University (17)
- Collyard Chiropractic P.A. (1)
- Colorado Hospital Association (6)
- Colorful Concepts Painting & Custom Finishing (1)
- CONCRETE INC (1)
- Conservation Job Board (1)
- Construction Jobs (2)
- Cooperative.com (1)
- Cornerstone Auto Group LLC (3)
- Cornerstone Building Brands (2)
- CorTech, LLC (1)
- Country Manor Campus (17)
- craigslist (19)
- Crawford Thomas (1)
- Cretex Companies (1)
- CRH (1)
- Crossmark (7)
- Crothall (1)
- CRYSTAL DISTRIBUTION (3)
- Culligan of Sauk Centre (1)
- CyberCoders (4)
- Dahl Consulting Inc. (16)
- Dairyland Peach (1)
- Dayton Freight LInes, Inc. (4)
- De jobs (9)
- Dependable Home Health Care (1)
- Dice (13)
- Dick's Sporting Goods, Inc. (1)
- Diedre Moire Corporation (1)
- Diocese of Saint Cloud (10)
- Disabled Person (98)
- Diversity Job Board (2)
- Diversity.com (10)
- Diversityjobs (143)
- DocCafe.com (8)
- DOHERTY (39)
- DOLLAR TREE (9)
- Dollar Tree Stores, Inc. (1)
- Dominium Management Services, Inc. (1)
- Domino's (15)
- DSW Inc. (1)
- dubow textile (5)
- Dycom (6)
- Eagle Creek Renewable Energy LLC (1)
- Eckroth Music (2)
- Eclaro International, Inc. (1)
- Ecumen (11)
- eFinancialCareers (1)
- Emerson Electric Co. (1)
- Employee-Owned Jobs (1)
- Energy Job Search (1)
- Energy Jobs Network (1)
- Entegee (1)
- ENTRUST Solutions Group (1)
- Essilor (11)
- Essilor and Subsidiaries (2)
- Fairview Health Services (5)
- FAR Inspections (3)
- Farmers Union Industries, LLC? (1)
- FashionJobs.com (14)
- Fastenal Company (2)
- Favorite Healthcare Staffing, Inc. (15)
- Federal Government Jobs (9)
- Ferche Millwork, Inc (2)
- Find jobs (4)
- Firestone Complete Auto Care (2)
- FIVE BELOW (2)
- FleetPride, Inc. (1)
- Foley Public Schools (1)
- ForceBrands (1)
- Fraser (6)
- Fresh Thyme Farmers Market (5)
- Furniture Mart USA (8)
- Fusion Medical Staffing, LLC (1)
- GameStop Corp. (4)
- GATR Truck Center (10)
- Geebo (2)
- Geo-Comm (2)
- Get Into Energy (2)
- Getting Hired (1)
- Good Shepherd Campus (13)
- GovernmentJobs.com (12)
- Grabjobs US (41)
- Great Clips, Inc. (12)
- Great River Federal Credit Union (1)
- GREAT Theatre (3)
- Greater St Cloud Area Chamber of Commerce (10)
- Green Thumb Industries (5)
- Guardian Angels Senior Services (30)
- Guardian Pharmacy (4)
- Guidant Financial (1)
- Gustave A. Larson Company (1)
- GXO Logistics (1)
- Hasbro (1)
- Health E-Careers (91)
- Health Inventures, LLC (4)
- Healthcare Recruitment Counselors (1)
- HealthJobsNationwide (28)
- Healthpartners, Inc. (4)
- Hershey Company (1)
- Higher Education Recruitment Consortium (85)
- HigherEdjobs (1)
- Hire Our Heros (1)
- HireRight, Inc. (1)
- HIREVeterans.com (10)
- Hiring Drivers Now (3)
- Hobby Lobby Stores, Inc. (1)
- Hog Slat, Inc. (1)
- Hom Furniture, Inc. (2)
- HomeDeliveryJobs (1)
- HomeGoods (1)
- Hormel Foods (7)
- HospitalCareers.com (8)
- HospitalRecruiting.com (2)
- HRT SOLUTIONS (1)
- Ichor Systems (40)
- iitjobs (2)
- IMDiversity (1)
- Independent School District 742 Comm Schools (46)
- INH Properties (2)
- Insomnia Cookies (2)
- Institute of Data (69)
- INTEGRITY STAFFING SOLUTIONS, INC. (1)
- Internships (3)
- Interstates Construction Services, Incorporated (3)
- IRET Apartments (4)
- J.C. Penney Company, Inc. (1)
- Jama Career Center (2)
- JBS (8)
- JD Home Healthcare (5)
- Jimmy John's (1)
- Jobs in Rigs (2)
- JobsHQ (24)
- JobsInLogistics (1)
- JobsInTrucks.com (9)
- JobSpider (44)
- JobVertise (1)
- John Deere (2)
- JOHNSON BROTHERS (1)
- Johnson Controls, Inc. (1)
- JPMorgan Chase & Co. (3)
- K12JobSpot.com (124)
- Kane Transport (1)
- Kelly Services, Inc. (5)
- KELOLandEmployment (9)
- Kerry (1)
- Keurig Dr Pepper (1)
- Kwik Trip, Inc (32)
- La-Z-Boy Inc. (5)
- Ladders (4)
- Land O'Lakes, Inc. (5)
- Landform Professional Services LLC (1)
- Law Firm Staff (1)
- Leaf Home (2)
- Learning Care Group, Inc. (7)
- Legacy Restoration (3)
- Lehighvalleylive (1)
- Lenscrafters (3)
- Levels.fyi (13)
- LGI Homes (1)
- Liberty Personnel Services, Inc . (2)
- LINDE (5)
- LocalJobNetwork (2)
- Locum Jobs Online (1)
- Lunds & Byerlys (3)
- lutheran social service of mn (6)
- Macy's, Inc (1)
- magnifi financial (1)
- Mains'l (1)
- ManpowerGroup (1)
- Mary T Inc. (1)
- Massage Envy (8)
- MasTec Network Solutions (1)
- Mayo Clinic (1)
- Media Bistro (1)
- MENARDS (5)
- MEP Jobs (2)
- Metal Craft (7)
- Metro Bus (4)
- Metro Sales, Inc. (2)
- Microbiologics (10)
- Midcontinent Communications (3)
- Midland Credit Management (1)
- Military Spouse Corporate Career Network (MSCCN) (1)
- militaryvetjobs (3)
- Millerbernd (5)
- MILLS FLEET FARM (4)
- Minnesota Credit Union Network (1)
- Minnesota NonProfits (4)
- Minnesota Paving & Materials (4)
- MinnesotaJobs (1)
- MinnesotaWorks.net (212)
- MN Sherburne County Jail (7)
- Moments Hospice (6)
- Monarch Healthcare Management (4)
- Monster (13)
- MPQ Inc (1)
- Nahan Printing (28)
- National Council for Behavioral Health. (1)
- National Guard (5)
- National Vision (2)
- Nations Roof (1)
- NDX Thoele (3)
- NEJM Career Center (1)
- Nexus (2)
- Noodles & Company (7)
- North Central Insurance Agency (1)
- North Memorial Health Care (3)
- Northland Capital (1)
- Northrop Grumman Corporation (2)
- Novelty, Inc. (1)
- NRG Energy, Inc. (1)
- Nurse.com (9)
- NurseJungle (2)
- Nutrien (2)
- Nystrom & Associates, Ltd (3)
- O'Reilly Automotive, Inc. (6)
- Ohio Means Jobs (2)
- OLD NAVY (1)
- Omaha World Herald (1)
- Operating Company","category":"Category","country":"Country","city":"City","state":"State","hireType (1)
- Optum (2)
- Orkin, Inc. (1)
- Palmer Group (3)
- Panera (1)
- Papa Murphy's Midwest (6)
- Penske Truck Leasing (1)
- Peopleready (3)
- Performance Foodservice (14)
- Petco (2)
- Phoenix School Counseling (1)
- PhysEmp (2)
- Pilot Flying J (4)
- Pomp’s Tire Service, Inc. (1)
- PostJobFree (2)
- Power to Fly (1)
- PracticeLink (23)
- PracticeMatch (2)
- Preferred Credit, Inc. (4)
- Pro Resources (1)
- Procore Construction Job Board (1)
- Product Connections (1)
- Professional Diversity Network (5)
- Propio Language Services (2)
- ProtoCall Services (1)
- Quanex Building Products Corporation (10)
- Qureos (5)
- R&M Manufacturing Co. (7)
- Radco Truck Accessories (1)
- Rain For Rent (3)
- Rasmussen College (4)
- RDO Equipment (6)
- RecruitMilitary (43)
- Red Robin (4)
- Redneck Trailer Supplies (1)
- Regional Help Wanted (2)
- Regis Corporation (4)
- RELX Group (1)
- Resume-Library (2)
- Retirement Jobs (23)
- RevPath (1)
- Richelieu Hardware (1)
- Ridgemont Resources Inc. (1)
- Rihm Kenworth (2)
- Rileighs Outdoor LLC (Vogel Display Corp) (1)
- River of Life Church (3)
- Robert Half (4)
- Rocori Public Schools (7)
- Rollins, Inc. (2)
- Ross Stores, Inc. (3)
- Rotochopper, Inc. (9)
- Royal Tire (1)
- Saint Cloud, MN (3)
- Sally Beauty Holdings (2)
- salon-on-main.net (1)
- Sam's Club (10)
- Sartell-St. Stephen Independent School District 748 (13)
- SCHEELS (20)
- Scholarshipdb.net (1)
- Seattle Times (2)
- Select Comfort Corporation (1)
- Sevita (10)
- Shared Medical Services (1)
- Sherburne County (3)
- Sherwin-Williams Company (2)
- Shields Health Solutions (3)
- Shopko Stores Operating Co, LLC (1)
- Sisters of the Order of Saint Benedict (2)
- Skechers (3)
- Snag (125)
- Soliant (1)
- Sorenson Communications, Inc. (3)
- SPAR, INC (3)
- SpartanNash (3)
- Spectrum (3)
- Spee-Dee Delivery Service, Inc (13)
- Spencer's Gifts (3)
- SST Direct (1)
- St. Cloud Municipal Athletic Complex (1)
- St. Cloud State University (1)
- Standard Iron & Wire Works (5)
- Standard Iron & Wire Works, LLC (3)
- Stanley Black & Decker, Inc. (2)
- Star Tribune Jobs (5)
- Starbucks Coffee Company (10)
- State of Minnesota (6)
- Stearns Bank (1)
- Steris Corporation (1)
- Structural Buildings (1)
- Stryker Corporation (1)
- Stuart C. Irby Company (1)
- stylecareers.com (1)
- Subway - 34611-0 (1)
- Subway - Sauk Centre (1)
- Sunbelt Staffing Solutions Inc (2)
- Surgical Care Affiliates, LLC (3)
- Synagro Technologies (1)
- Syngenta (1)
- T-Mobile (6)
- TalentAlly (4)
- TAMU Natural Resources Job Board (1)
- Tandym Group (1)
- tapwage (2)
- Tapwage_US (101)
- Target Corporation (1)
- Team Work Online (1)
- TechCareers.com (1)
- TelCom Construction, LLC (6)
- The Bank of Elk River (2)
- The Buckle (5)
- The College of St. Scholastica (1)
- The Good Shepherd Community (1)
- The Gypsy Nurse (9)
- The Job Network (31)
- The Lauridsen Group (2)
- The Muse (1)
- The Nielsen Company (1)
- THIES & TALLE MANAGEMENT CO INC (1)
- Thrivent Financial for Lutherans (1)
- TipTopJob Group (9)
- TJ Maxx (4)
- TKC Holdings, Inc. (1)
- TOTALMED (2)
- Townsquare Media (3)
- Tractor Supply Company (2)
- Tradesmen International (1)
- Tri-County Action Program (Tri-CAP) (4)
- Trillium Staffing (1)
- Trustaff (2)
- TweetMyJobs (22)
- U-Haul (8)
- U.S. Foodservice, Inc. (1)
- Ulta Salon, Cosmetics & Fragrance, Inc. (6)
- United Rentals, Inc. (1)
- United Way of Central Minnesota (4)
- University Of Minnesota (1)
- US.jobs (176)
- USAJOBS (19)
- Valvoline (3)
- vbeyond corp (1)
- Verizon Communications Inc. (2)
- Vestis Corporation (2)
- Viking Coca-Cola (17)
- VitaminShoppe (1)
- Vivian (3)
- Vivo HealthStaff (1)
- Vogel Display Corp. (1)
- Walgreens Company (11)
- Walmart (37)
- Wanderly (29)
- Waste Management Corporation (1)
- Water guards (1)
- WayUp (4)
- Wells Fargo & Company (2)
- Westaff (9)
- WestRock Company (1)
- WESTWOOD PROFESSIONAL SERVICES (8)
- Wireless Vision, LLC (1)
- WIS International (4)
- Wolters Kluwer (7)
- Workplace Diversity (1)
- Wright Medical Group (1)
- WSB & Associate Inc (3)
- YMCA of St Cloud (9)
- Zeiss (1)
- Ziegler Inc. (3)
- Zimmerman Physical Therapy (1)
- ZippyApp (1)
- ZOLL LifeVest (1)
- Zoll Medical Corporation (1)
Jobs listed here are collected daily from online employer and aggregate job boards, pulling jobs from the three counties of Stearns, Benton and Sherburne.
Learn More ›
Learn More ›
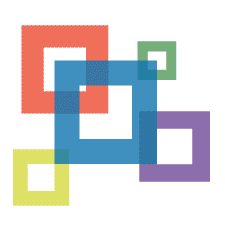